Printed Matter
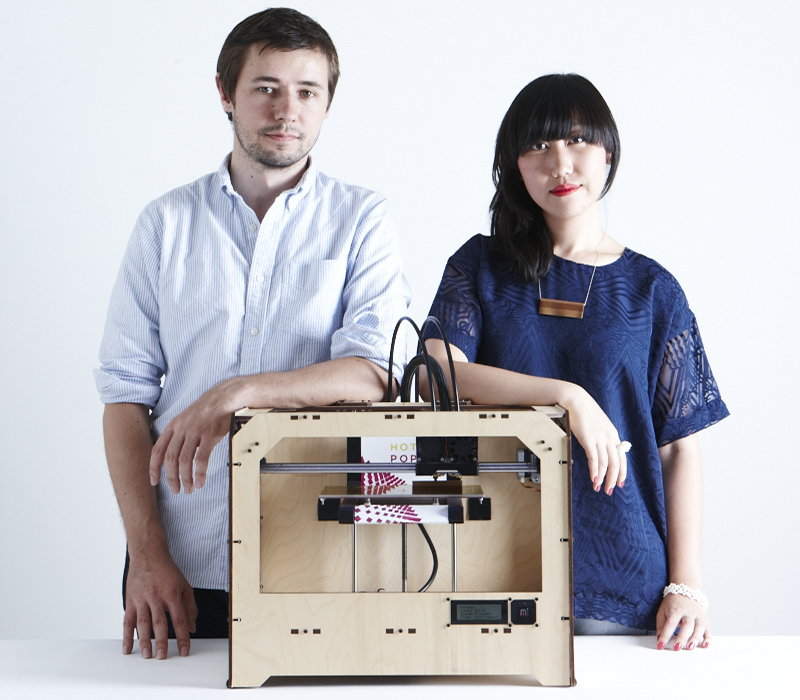
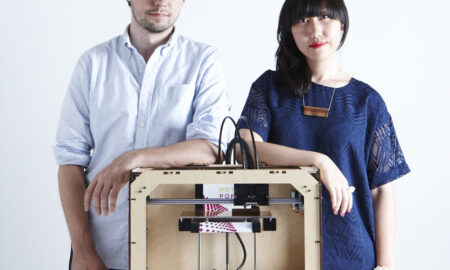
Wearable art: fashions gets the 3-D treatment with a new line of digitally printed jewellery
Inside Hot Pop Factory’s west end studio, a necklace slowly takes shape under an electric nozzle, humming as it moves back and forth. In a nod to Dutch graphic artist M. C. Escher, the end result will feature sleek, fanning geometry in polymer: wearable art made entirely with a 3‑D printer, no bigger than a microwave, in just under an hour.
For independent designers, this is no longer the stuff of science fiction. Now relatively affordable, accessible and virtually instantaneous, 3‑D printing stands in stark contrast to the multi-stepmanufacturing processes of old. The technology’s commercial ubiquity, which may be closer than you think, will enable a rising generation – that includes University of Waterloo School of Architecture graduates and Hot Pop owners Matt Compeau and Bi-Ying Miao – to produce original and inventive designs.
Hot Pop’s products walk a fine line between architecture and fashion. Compeau and Miao conceive of their creations with 3‑D modeling software, often used by architects, that they’ve customized with algorithms capable of generating any sequence of geometric shapes or patterns.
Another of their pendants – made from German-engineered cherrywood that’s been pulverized and mixed with a polymer – boasts a subtle curvature and striations caused by changing the temperature of the printer’s nozzle. The pair happily discovered this technique while experimenting with the manufacturing, which begins when the thinned and spooled wood is fed and heated through the printer (Miao likens the process to building layers with a glue gun, although here the expelled bead is a fraction of a millimetre in size). All this happens on a calibrated platform that lowers incrementally with every layer applied. It takes 45 minutes to print the striated piece.
“There are no moulds; repeatability in the manufacturing process isn’t necessary,” says Compeau. “That means there’s no reason not to customize everything for the individual who’s buying it.”
Manufactured on a printer from Brooklyn-based Makerbot, Hot Pop’s jewellery is essentially the result of digital design code – infinitely changeable, theoretically open-source, and easily downloadable. Much like file sharing of digital music, movies and books, the advent of 3‑D printer technology could pose problems for designers: perhaps one day soon we’ll be searching torrents for an original table and chair set. It’s a worrying thought. But Compeau and Miao aren’t nervous; downloading will just encourage them to keep innovating. The duo has recently connected with a manufacturer that prints nylon, allowing for even more textile choices. Coming soon: home accessories and possibly furniture.